In the third of our series of interviews with players in the gas fermentation space (read about Calysta and Circe here and here), we spoke to Unibio, a Danish firm using methane to feed its protein-packed bacteria for feed and food.
Based in Copenhagen, Unibio has developed a patented vertical ‘U-Loop’ bioreactor designed to maximize gas/liquid transfer in a continuous biomass fermentation process.
It has raised around $120 million to date, $70 million of which came from Saudi Industrial Development Group in 2023, no mean feat given that this was a “very dead time in terms of raising money,” observes CEO David Henstrom.
AgFunderNews (AFN) caught up with Henstrom (DH) to talk about the pros and cons of using gases, rather than sugars, to feed microbes, and why the firm is turning to the Middle East for funding and partnerships…
AFN: You joined Unibio at a somewhat challenging time…
DH: The technology has been under development for some time, but I joined in the summer of 2021 just as the first commercial industrial scale facility was just getting started in Russia [by licensee Protelux] to sell to European clients.
So we were out there raising money and right in the middle of a number of discussions when Russia invaded Ukraine [in February 2022]. People were scrambling to look at their portfolios and at any exposure they might have and things went pretty quiet, so we had to pivot and start development in other areas.
As far as we understand, the plant [in Russia] is still running, but it operates within all the sanctions regimes [instituted after the invasion]. Given the situation, it’s difficult for us to provide significant guidance and direction and help to them.
AFN: So what’s your focus now?
DH: Another licensee of our technology is [biotech investor] Gulf Biotech so we’re busy working with them on a partnership in Qatar [which is rich in natural gas resources but has little farmland on which to produce protein] and trying to get that through to a final investment decision.
We’re also working with the Saudi Industrial Development Group, which is a major investor, and we’re looking at a project with them, but we haven’t announced anything more yet.
We’re looking all around the world at where there is cost effective gas, oxygen, ammonia [as inputs], and the infrastructure to put up facilities to produce protein that is also proximate to the demand that we’re going after.
The Middle East is really interesting on this front. Saudi Arabia is almost 100% feed insecure; it imports most of its ingredients to feed animals. The benefit of having these [gas fermentation] plants is that you can put them in deserts, in frigid locations, basically in places where crops won’t necessarily grow.
We’re also seeing interest in our reactor technology that goes beyond protein production. People are interested in using it to produce other chemicals and materials and we’re in discussions with a number of companies on that front.
I call this “gas to x opportunities” where we have the reactor technology, that is the hardware. The microbes, which you might call the software, could be developed by another company. You put the two together and see how efficient the combination is versus alternate approaches [to producing the same materials].
AFN: What’s the Unibio business model?
DH: Licensing is our model first and foremost, because we need to manage the balance sheet, although we do also look at joint ventures. But what makes us unique is that we have the front end, the technology, while our licensing and/or joint venture partners have the back end [building the plants], but we also can handle the sales to end customers in animal feed, pet food and ultimately human food.
We could also do a co-investment model where we might put some equity into a facility with a partner.
AFN: What markets are you targeting with your protein?
DH: We already have regulatory approval for Uniprotein [Unibio’s branded ingredient] for feed and pet food in Europe, and feed in some Asian countries including Japan and Thailand. And then food is also in the early stages of regulatory approval.
For [human] food approval, the US and Europe would be our two target areas, with maybe a start in Singapore.
On the aquaculture side, we’ve done a number of studies and Uniprotein compares very favorably vs fishmeal on feed conversion rates; it’s a highly concentrated protein with high digestibility. I’m not an expert on insect protein [which is being targeted at the aquaculture market] but there are palatability issues we’re aware of there, plus the costs are challenging if you want to get into mainstream aquaculture applications.
AFN: If gas fermentation is a no brainer, why isn’t everyone doing it?
DH: There certainly are a number of companies [in gas fermentation for protein] that are at an earlier stage than us. We’ve learned a lot, we have multiple patent families and a lot of trade secrets and operational know-how that has come from the years we’ve been at this, which I think really distinguish us right now. But there are barriers to entry, plus you have to deal with the capital costs of building new facilities, which can be substantial.
AFN: How are investors looking at this technology?
DH: We were fortunate to have one of the largest raises in the alternate protein sector in 2023 [$70 million] in March [from Saudi Industrial Development Group], which was a very dead time in terms of raising money. I’d say sovereign wealth funds certainly are interested in this technology, plus large family offices. It’s late-stage growth equity.
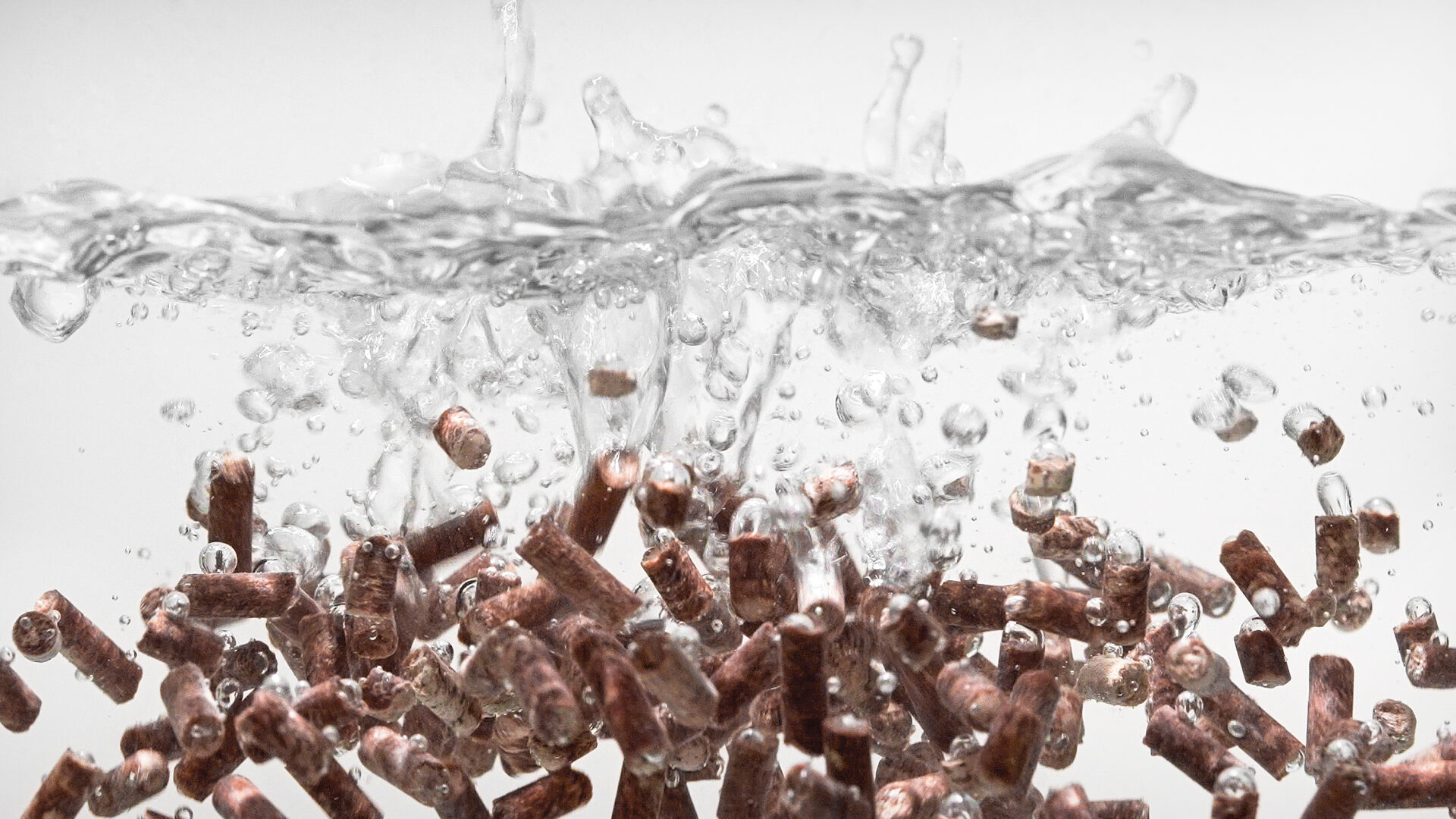
AFN: Talk me through the basics of the technology…
DH: We’re growing a Non-GMO bacterium, a methanotroph [a microorganism that metabolizes methane as its primary source of carbon and energy] that naturally produces a lot of high-quality protein. We grow it, harvest the whole biomass, centrifuge it, and dry it.
For inputs we need methane, oxygen, nitrogen from an ammonia source, and some salts. For the bioreactor you need to have the right design to get optimal gas liquid transfer, which is why I think it has has taken this technology some time to evolve to where it is today. Figuring out how best to do that requires real ingenuity.
We inject the gases into the water stream with the bacteria and they produce protein as they go around that loop and then we harvest it.
AFN: What’s the thinking behind the U-Loop bioreactor design?
DH: We think we have the most efficient reactor design for gas fermentation. One of the benefits of the U-Loop design is that you can take advantage of the mass transfer [the movement of gases from the gas phase into the liquid phase], with the pressure that’s in a vertical system versus a horizontal system.
That helps the bubbles stay in solution rather than accumulate, for example, at the top of a horizontal system.
AFN: Why is gas fermentation potentially more efficient or sustainable than using sugary feedstocks?
DH: Coming from Cargill, I was trained in sugar-based fermentation. With gas fermentation, we’re converting a non-edible abundant source of carbon into protein, and we’re not using any land [to grow corn or other sources of sugars for fermentation].
If you just look at the cost of carbon per ton of protein that you produce, it’s three times the cost to use glucose or dextrose vs methane. And then there isn’t the same risk of contamination [from unwanted microbes that feed on sugar]. This means you can run longer campaigns and run a continuous fermentation, which has its own set of benefits.
AFN: How will the methane be sourced for Unibio plants?
DH: At our demo facility in Denmark, we use 100% biogas there [as a methane source], because the industry is so well developed in Denmark that it’s fairly cost competitive.
You can get methane from a number of sources; for example you can [use electrolysis to] split water into hydrogen and oxygen, and then do a methanation process on the hydrogen [to convert it into methane].
However, in the places we’re currently looking to deploy, natural gas is the first option as it’s abundant.
Further reading:
Can gas fermentation deliver on its green promise for food and feed? In conversation with Calysta
Aerobic gas fermentation: the final frontier in novel fats?
🎥Biomass fermentation in focus at MISTA growth hack: ‘The food of the future is going to be manufactured in a tank’
Gas fermentation co LanzaTech enters food arena: ‘We’ve developed a path to mass producing protein from CO2’
Source link
Author Elaine Watson