With demand for cocoa and coffee expected to dramatically exceed supply as climate change impacts key growing regions, a flurry of solutions has emerged from bean-free alternatives from upcycled date seeds to more robust coffee plants .
The next wave of startups is growing “real” coffee and cocoa biomass from plant cell culture, an approach that has started to attract the attention of strategic investors from Mondelēz International (which has invested in Celleste Bio and included Kokomodo in its CoLab Tech accelerator cohort ) to Puratos (which has invested in California Cultured via its corporate venture arm Sparkalis).
Rather than using sunlight, water, and soil to nurture fully-grown plants, firms using plant cell culture grow plant cells indoors in bioreactors fed on sugars, vitamins, minerals, and other nutrients.
The approach is already used on a commercial scale to produce a handful of drugs, notably breast cancer drug Taxol. And while commodities producing such as coffee and cocoa is a very different ballgame, the unit economics still make sense, insists Christian Schaub, CEO at Zurich-based plant cell culture startup Food Brewer .
“We have collaborations with global coffee, chocolate, and food companies who have approached us because they need to secure these resources for the future at scale, and we are very confident that this is scalable.”
Scaling up plant cell culture
According to Food Brewer CFO Mathilde Dupin: “Our initial focus is on being a b2b ingredients supplier. We’re already at pilot scale [800-liter bioreactor producing kilos of product] and our next goal is to get to demo-scale either by retrofitting a brewing facility or partnering with clients with production capabilities that can be adapted.
“We see the first large-scale plants as, say, 50,000 liters, but down the road it could go bigger. Plant cell culture has already been proven commercially at 75,000-liter scale.”
Food Brewer is currently working with beverage production equipment giant Krones on adapting equipment from the brewing industry rather than the biopharma industry in order to keep costs down, adds Schaub.
“You need a system that you can run for long periods of time without a lot of maintenance, that’s easy to clean, and involves a lower capex investment, which is why we started looking into retrofitting non sterile steel systems from other industries.”
One obvious advantage of plant cell culture versus precision fermentation is that firms are harvesting the whole biomass , rather than engaging in costly downstream processing to extract and purify ingredients, notes Schaub. “We don’t have to get rid of the host [microorganism], we’re basically just growing cells, collecting the biomass and drying it.”
And unlike cell culture media for cultivated meat , he says, “We only pay a few cents per liter [for the media, which is primarily composed of sugars plus minerals, vitamins, and plant growth hormones].”
The focus is on optimizing the cell lines and cell culture media to ensure the most cost-efficient process, an approach aided by Food Brewer’s partnership with Fruitful Ai , which has developed an automated cell selection and media screening platform, adds Schaub.
“We’ve filed a patent application covering our unique method to establish stable cell lines [that can grow in liquid suspension in a bioreactor as opposed to on a petri dish] very quickly.”
The approach also means that Food Brewer can also work with rare coffee or cocoa varieties with particular characteristics that may not be suitable for mass cultivation as fully grown plants but can flourish in plant cell culture, he notes.
Post-harvest parameters
While Food Brewer is spending a lot of time and energy on optimizing cell lines, media, and the conditions inside the bioreactor, he says, much of the work that contributes to the flavor and aroma of its coffee and coconut is done post-harvest during the fermentation and roasting steps.
“We conduct [chemical] analyzes of the coffee at the ‘green’ stage (the harvested biomass), after roasting, and at the brewed stage and fine tune the profile to have something that is really delicious.”
The caffeine content of coffee from plant cell culture tends to be lower than in coffee from beans, he notes, in part because the plant cells are not exposed to the same stressors as fully-grown plants. But this can be a plus at a time when many consumers are looking for the experience of real coffee, without so much caffeine.
Regulatory, labeling, and go-to-market strategy
Food Brewer is initially targeting the US market and aims to file GRAS (Generally Recognized as Safe) notifications with the FDA this year with a view to market entry in late 2026, says Schaub.
On labeling, he says, “Obviously, what we harvest from coffee cell culture is coffee, but we’re talking to the FDA and to our advisors about how best to communicate what we’re doing, and labeling is still to be determined.
“There’s a chance that cocoa will be the first [product from Food Brewer to hit the market], which has to do with the existing partnerships we have in place. But as we speak, we’re also looking into collaborations with major coffee players, and if they decide to go faster, maybe we hit the market first with coffee.”
The funding environment
To date, Food Brewer has raised over CHF5 million in pre-seed equity and is about to close a new round from financial and strategic investors, says Schaub. “We’ve also had research contributions coming from our clients directly.”
Some investors need educating on the nuances of plant cell culture and how it differs from cultivated meat, which has a very different pricing structure, he claims. However, they can all see the benefits of biomass vs precision fermentation, says Schaub. “We’re not spending money on extraction and purification.”
Stepping back to look at the bigger picture, says Dupin, “Investors can see that certain crops are subject to the impacts of climate change and it is just becoming more and more obvious that these impacts on availability and pricing will be long lasting.”
According to Schaub: “We’re not trying to replace agriculture or even compete with it; we’re just closing the gap between demand and agricultural supply.”
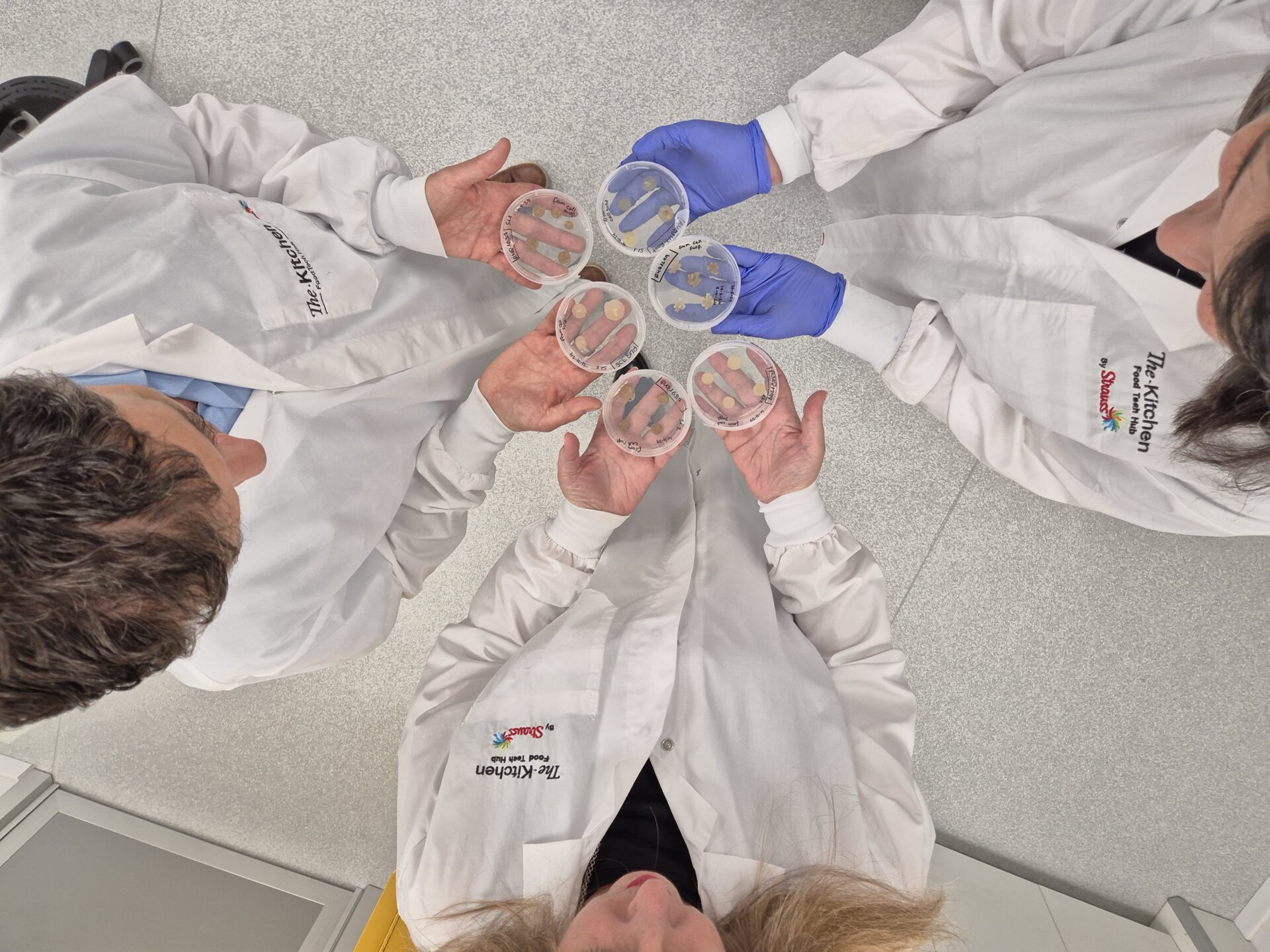
Pluri acquires controlling stake in Kokomodo
His comments came as Israeli firm Pluri —which has developed proprietary packed bed bioreactors for growing animal and plant cells at subsidiaries including Ever After Foods (cultivated meat) and Coffeesai ( coffee plant cell culture )—acquired a controlling stake in cocoa plant cell culture startup Kokomodo .
The acquisition, which followed a $6.5 million investment from global investor Alejandro Weinstein, will enable Kokomodo to tap into Pluri’s expertise and more rapidly scale up its technology, Pluri CEO Yaky Yanay told AgFunderNews .
“The first cost estimates that we have applying Pluri’s technology into the production of Kokomodo cacao are very promising and will give Kokomodo a tremendous competitive advantage in this vertical.”
Asked about scaling plant cell culture, he added: “From day one, we have been growing cells in packed bed reactors that allow us to achieve real scale in relatively small bioreactors as our system is 20 times more efficient than a [typical] steel bioreactor [where cells grow in suspension].
“Our plan is to move aggressively and quickly to bring these solutions to market and our first step is to use bioreactors with five chambers of 200 liters capable of producing hundreds of kilos of cocoa and coffee. We anticipate that in 2026 this system will be available from Pluri for manufacturing across our subsidiaries. So when I’m talking about scaling up, it’s not a 10-year process, this is something that we see coming and coming soon.”
He added: “We are already discussing with players in the [coffee and chocolate] industry that are showing very significant interest in our solutions.”
Weinstein explained: “This is one of those rare opportunities you find in life as an investor, when you look at the quality of the people and the technology, it’s quite unique. The potential is explosive.”
Further reading:
ReaGenics deploys plant cell culture to create potato biomass with 31% protein content
Plant cell culture deep dive: As cracks emerge in botanical supply chains, ‘It’s a huge space to watch’
Sparkalis Invests in plant cell culture startup California Cultured to futureproof cocoa supply chain
Real cocoa… without the beans? Kokomodo deploys plant cell culture to tackle cocoa supply challenge
Source link
Author Elaine Watson